LEAN 4.0: Áp dụng một số công cụ Quản lý tinh gọn trong Công nghiệp 4.0
(CL&CS)- Áp dụng một số công cụ Quản lý tinh gọn trong Công nghiệp 4.0
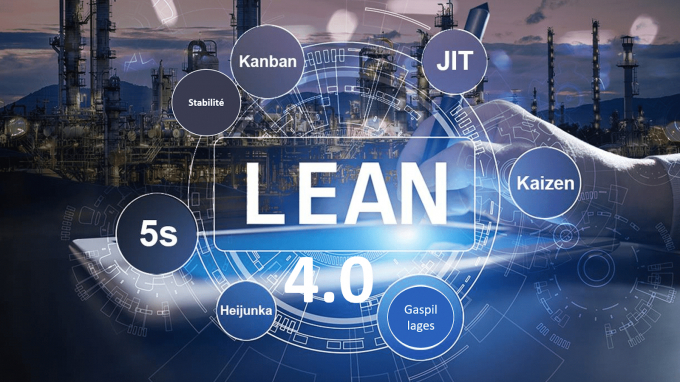
1. Đúng thời điểm/ Đúng trình tự 4.0 [Just-In-Time (JIT)/ Just-In-Sequence (JIS) 4.0]
JIT xuất phát từ Nhật Bản và được phát minh bởi Kiichiro Toyoda và Taiicho Ohno vào năm 1950. Giữa tất cả những hệ thống quản lý khác, JIT đã được áp dụng thành công trong nhà máy Toyota, và mang đến sự tăng trưởng vượt bậc cho năng suất. JIT dựa trên hệ thống Kanban, một quy trình phục vụ hậu cần và sản xuất bằng cách sử dụng các tín hiệu như thẻ màu, bảng hiệu, cờ hoặc đèn.
Phương pháp JIT được sử dụng để xác định số lượng hàng tồn kho. Bằng cách sử dụng đúng ứng dụng, tính hiệu quả, chất lượng và độ tin cậy trong công ty sẽ tăng lên. Việc phân phối và sản xuất cần phải được đồng bộ hóa sao cho hàng tồn kho cần giữ là ít nhất có thể.
Phương pháp tinh gọn JIT/JIS nhằm mục đích cung cấp đúng sản phẩm, đúng thời điểm, địa điểm và chất lượng với số lượng phù hợp với chi phí phù hợp.
Một số công cụ Công nghiệp 4.0 có thể đóng góp thực hiện mục tiêu này như được nêu trên.
Chẳng hạn, công cụ xe hướng dẫn tự động (Automated guided vehicles, AGV) có thể tự động vận chuyển các đối tượng theo định hướng. Điều này giảm thiểu các vận chuyển “sai sót” do tác động của con người. Trong trường hợp có chướng ngại vật, hệ thống vận chuyển sẽ tự động dịch chuyển theo một hướng đi khác.
Bên cạnh công cụ xe hướng dẫn tự động, các thùng, sản phẩm thông minh (intelligent bins and smart products) được tự tối ưu hóa nhờ Công nghiệp 4.0. Bộ nhớ kỹ thuật số trong các thùng, sản phẩm thông minh sẽ lưu trữ các tham số sản xuất cần thiết để điều hướng các phương tiện vận chuyển tự động một cách hiệu quả nhất. Công nghiệp 4.0 giúp doanh nghiệp xây dựng mạng lưới logistic mạnh để phục vụ sản xuất.
Ngoài ra, công nghệ nhận dạng tự động Auto-ID (như Nhận dạng qua tần số vô tuyến-RFID…) có thể được áp dụng để theo dõi vật liệu theo thời gian thực và định vị chính xác các đối tượng trong chuỗi giá trị. Điều này giúp doanh nghiệp giảm thời gian tìm kiếm và cải thiện tính minh bạch của quy trình. Công nghệ này cũng cho phép xác định loại bỏ các thành phần không cần thiết trong chuỗi giá trị. Việc lựa chọn tự động nhờ thẻ RFID cho phép theo dõi các vật liệu, sản phẩm một cách liên tục, qua đó làm giảm mức độ tồn kho của doanh nghiệp. [N. Fescioglu-Unver, S. Choi, D. Sheen and S. Kumara, “RFID in production and service systems: Technology, applications and issues,” Information Systems Frontiers, vol. 17, no. 6, pp. 1369-1380, 2015].
Phương pháp JIT/JIS 4.0 áp dụng công nghệ phân tích dữ liệu và dữ liệu lớn để phân tích chi tiết thông tin quy trình theo thời gian thực, cung cấp các tham số giúp xác định xu hướng chính xác hơn, qua đó doanh nghiệp thực hiện điều chỉnh hệ thống sản xuất [K. Ding and P. Jiang, “RFID-based production data analysis in an IoT-enabled smart job-shop,” IEEE/CAA Journal of Automatica Sinica, pp. 1-11, 2017].
Phân tích dữ liệu lớn giúp doanh nghiệp thực hiện hoạt động sản xuất liên tục nhờ khả năng dự đoán bảo trì máy móc, thiết bị. Giảm thời gian ngừng hoạt động của máy đóng góp tăng hiệu suất của doanh nghiệp trong toàn bộ chuỗi cung ứng [G. Srinivasan and G. Ganesh Prasad, “The role of Intelligent Automation, Big Data and Internet of Things in Manufacturing - A Survey,” Imperial Journal of Interdisciplinary Research, vol. 3, no. 5, pp. 934-940, 2017].
Nhìn chung, JIT/JIS 4.0 giúp cải thiện tính linh hoạt và giảm thời gian thực hiện mục tiêu cung cấp đúng sản phẩm, đúng thời điểm, địa điểm và chất lượng với số lượng phù hợp.
2. Cân bằng dây chuyền sản xuất 4.0 (Heijunka 4.0)
Phương pháp cân bằng dây chuyền sản xuất (Heijunka) là phương pháp sản xuất để cân bằng giữa loại sản phẩm và lượng sản xuất của quá trình lắp ráp cuối cùng, nhằm điều chỉnh quá trình sản xuất theo sự thay đổi của yêu cầu khách hàng. Heijunka là một trong những công cụ để đạt được trình độ sản xuất JIT. Đó là kỹ thuật để giúp loại bỏ các lãng phí dựa trên nguyên tắc: Tạo ra sản phẩm trung gian theo một tốc độ ổn định nhằm cho phép quá trình tiếp theo cũng được thực hiện theo một tốc độ ổn định và có thể dự báo trước được.
Mục tiêu của Heijunka là “cân bằng”, điều chỉnh sản xuất, bằng cách chỉ sản xuất theo nhu cầu của khách hàng, giảm mọi lãng phí, dư thừa trong sản xuất.
Một số công cụ Công nghiệp 4.0 góp phần cải thiện Heijunka. Ví dụ: Phân tích dữ liệu lớn giúp nâng cao chất lượng dự báo. Việc lập kế hoạch sản xuất của doanh nghiệp được “cân bằng” ổn định nhờ sử dụng dữ liệu kết hợp với sự hiểu biết tốt hơn về nhu cầu của khách hàng và các phân tích chuyên sâu về thị trường.
Một số công cụ phần mềm dựa trên công nghệ thông tin mới được phát triển để sử dụng hỗ trợ quá trình lập kế hoạch của doanh nghiệp. Ví dụ, phần mềm AnaPro tự động cung cấp chương trình, kế hoạch sản xuất dựa trên thông tin về quy trình công nghệ, đặc điểm kỹ thuật sản phẩm, địa điểm sản xuất, kinh doanh… [K. Zywicki, P. Rewers and M. Bozek, “Data Analysis in Production Levelling Methodology,” in Recent Advances in Information Systems and Technologies, Á. Rocha, A. M. Correia, H. Adeli, L. P. Reis and S. Costanzo, Ed. Cham, Switzerland: Springer International Publishing, 2017, pp. 460-468].
Áp dụng lợi ích Heijunka 4.0 nhằm giảm thiểu sản xuất thừa, cân bằng chương trình sản xuất thông qua việc lập kế hoạch tự động và điều chỉnh “linh hoạt” để đáp ứng yêu cầu khách hàng và thị trường.
3. Kanban 4.0
Kanban là một công cụ để vận hành hệ thống JIT. Đó là một chiếc nhãn hoặc thẻ, thường được bọc bên trong một bao bì nhựa. Trên Kanban, thường chứa những thông tin sau: Tên chi tiết, sản phẩm được sản xuất; sức chứa của thùng Kanban; địa chỉ, ký hiệu của quy trình làm việc trước; địa chỉ, ký hiệu của quy trình sau. Ngoài các thông tin chủ yếu đó, thì tuỳ vào loại Kanban và tuỳ vào tình hình cụ thể của mỗi doanh nghiệp mà có thể có thêm những thông tin khác.
Kanban đặt mục tiêu duy trì dòng nguyên liệu liên tục bằng cách duy trì mức tồn kho được xác định trước để đảm bảo nguồn cung nguyên liệu không bị gián đoạn.
Công nghiệp 4.0 có thể góp phần tăng cường phương pháp quản lý tinh gọn này.
Áp dụng công nghệ mô phỏng theo thời gian thực, các vòng lặp kanban mới có thể được tích hợp vào hệ thống sản xuất hiện có. Công nghệ mô phỏng đảm bảo xác định các thông số kanban một cách chính xác hơn.
Công nghệ Auto-ID giúp doanh nghiệp theo dõi các hoạt động liên tục của quá trình. Do đó, tính minh bạch của các dòng vật liệu trong quy trình sản xuất được tăng lên, qua đó loại bỏ các vật liệu không cần thiết trong quy trình. Mức nguyên liệu có thể được giảm đến mức tối thiểu.
Áp dụng các công cụ Công nghiệp 4.0 trong Kanban, mức độ sử dụng nguyên liệu có thể được giảm thiểu, qua đó sẽ giúp doanh nghiệp tiết kiệm chi phí.
4. Lưu đồ chuỗi giá trị 4.0 (Value Stream Mapping- VSM 4.0)
Bất cứ một hoạt động nào mà không mang lại giá trị cho thành phẩm cuối cùng đều được coi là lãng phí. Để phát triển được trong thị trường khốc liệt ngày nay, doanh nghiệp phải chắc chắn đạt được và duy trì được sai số ở mức 0 trong quá trình kinh doanh. Phương pháp lưu đồ chuỗi giá trị (VSM), một dạng framework cao cấp của mô hình quản lý tinh gọn để cải tiến quy trình, xác định và loại bỏ lãng phí trong hoạt động của doanh nghiệp.
VSM là một hệ thống các phương pháp và công cụ nhằm giảm thiểu lãng phí, giảm thiểu thời gian không gia tăng giá trị, từ đó giảm thiểu thời gian sản xuất. VSM tăng cường tính minh bạch của luồng vật liệu và thông tin trong chuỗi tạo giá trị.
Công nghiệp 4.0 dẫn đến một môi trường sản xuất được kết nối nơi dữ liệu có thể được truyền trong thời gian thực. Công nghệ dữ liệu lớn và phân tích dữ liệu tạo điều kiện thuận lợi cho việc hợp nhất thông tin, qua đó hỗ trợ việc đưa ra các quyết định dựa trên điều kiện thực tế.
Áp dụng các thiết bị tương tác giữa người và máy tính (Human-Computer Interaction, HCI) cho phép nhận thông tin, kích hoạt các hoạt động và quy trình kiểm soát từ xa để tối ưu hóa quy trình. Ví dụ, Công nghiệp 4.0 hỗ trợ nhân viên bảo trì theo dõi việc bảo trì máy móc, thiết bị từ xa để nâng cao hiệu suất máy, giảm thời gian “chết” hoặc không sử dụng của máy móc, thiết bị.
VSM 4.0 là một công cụ để giúp doanh nghiệp quản lý hoạt động hàng ngày nhằm giảm thiểu lãng phí, giảm thiểu thời gian không gia tăng giá trị. Máy học và phân tích dữ liệu lớn hỗ trợ tạo ra một dòng giá trị của doanh nghiệp thông qua việc xác định mục tiêu và tự động triển khai thực hiện. Cách tiếp cận này hỗ trợ quá trình cải tiến liên tục.
Lợi ích chính của VSM 4.0 là cải thiện tính minh bạch thông qua hiển thị thời gian thực các dòng giá trị. Điều này giúp xác định lãng phí trong các quy trình sản xuất và dẫn đến việc tạo ra giá trị quản lý tinh gọn.
5. Duy trì hiệu suất thiết bị tổng thể 4.0 (Total productive maintenance- TPM 4.0)
Duy trì hiệu suất thiết bị tổng thể (TPM) là một phương pháp quản lý được áp dụng đầu tiên tại Nhật Bản, sau đó được phổ biến, áp dụng rộng rãi trong các ngành sản xuất công nghiệp trên toàn thế giới. Theo phương pháp này, người lao động vận hành phải đảm nhiệm cả công việc bảo dưỡng hàng ngày, còn bộ phận bảo dưỡng chuyên trách sẽ quản lý và đảm nhiệm các công tác bảo dưỡng quan trọng định kỳ. Khái niệm tự chủ bảo dưỡng (Autonomous Maintenance, AM) là một yếu tố quan trọng của TPM.
Việc thực hiện TPM là nhằm tối đa hóa hiệu suất thiết bị, nâng cao năng suất với một hệ thống bảo trì được thực hiện trong suốt vòng đời của thiết bị, đồng thời nâng cao ý thức và sự hài lòng với công việc của người lao động. Với TPM, mọi người cùng hợp lực và tương tác với nhau để nâng cao hiệu suất hoạt động của thiết bị một cách hiệu quả nhất.
Trong Công nghiệp 4.0, số lượng đối tượng máy móc, thiết bị cần bảo trì trong nhà máy thông minh (Smart Factory) ngày càng tăng. Độ phức tạp kỹ thuật và các sự cố đột xuất về máy móc, thiết bị thường làm doanh nghiệp phải chịu các chi phí cao trong sửa chữa. Do đó, các hoạt động liên quan đến bảo trì sản xuất cũng được xác định là một hệ thống quản lý toàn diện.
Vòng đời sản phẩm ngắn hơn, sự đa dạng sản phẩm cao hơn và độ phức tạp của sản phẩm và dây chuyền sản xuất ngày càng tăng. Do đó, năng lực của các chuyên gia bảo trì gắn liền với việc thực hiện các biện pháp bảo trì phòng ngừa (hay còn gọi là bảo trì theo kế hoạch).
Một số công cụ Công nghiệp 4.0 hỗ trợ hoạt động TPM. Đặc biệt, sự kết hợp của các công nghệ như thực tế ảo (Virtual Reality, VR) và thực tế tăng cường (Augmented Reality, AR) tạo điều kiện cho hoạt động đào tạo, hướng dẫn bảo trì. Do đó, các chuyên gia bảo trì có thể thực hiện các hoạt động bảo trì thông qua các phương pháp tương tác từ xa [S. Benbelkacem et. al., “Augmented Reality Platform for Collaborative E-Maintenance Systems,” in Augmented Reality - Some Emerging Application Areas, A. Y. C. Nee, Ed. London, UK: InTech, 2011].
Hơn nữa, các sản phẩm thông minh và công nghệ trong Công nghiệp 4.0 cho phép tự giám sát, đánh giá liên tục về hoạt động, hao mòn và các “sai sót” của máy móc, thiết bị trong quá trình vận hành. Việc phát hiện và xác định sớm giúp giảm đáng kể thời gian “chết” của thiết bị, máy móc, qua đó ngăn ngừa thiệt hại do công tác bảo trì gây ra. [A. Jardine, D. Lin and D. Banjevic, “A review on machinery diagnostics and prognostics implementing condition-based maintenance,” Mechanical Systems and Signal Processing, vol. 20, no. 7, pp. 1483- 1510, 2006].
Công nghệ phân tích, dự báo là một công cụ hữu ích để bảo trì thiết bị, máy móc theo kế hoạch vì công nghệ này cho phép phân tích mối tương quan giữa các tham số điều kiện và xác suất. Công nghệ phân tích, dự đoán sử dụng các thuật toán phức tạp để dự đoán lỗi dựa trên dữ liệu lớn. Công nghệ phân tích, dự đoán sẽ dự kiến chính xác về tuổi thọ của máy móc, thiết bị. Với phương pháp tiếp cận này, Lucke và cộng sự đã đề xuất một hệ thống bảo trì thông minh để tăng tính khả dụng và giảm chi phí bảo trì cũng như tiêu thụ năng lượng.
Trong quản lý sản phẩm và thiết bị, công nghệ số hóa góp phần loại bỏ sự gián đoạn truyền thông giữa các giai đoạn lập kế hoạch và thiết kế và giai đoạn sản xuất. Công nghệ “Plug and play” cho phép tích hợp tự động hệ thống kỹ thuật dựa trên các thiết kế mô-đun định hướng dịch vụ. Do đó, các nhà máy sản xuất có thể dễ dàng được điều chỉnh và tùy chỉnh hệ thống thiết bị phù hợp với hoạt động sản xuất và bảo trì.
6. Chuyển đổi nhanh 4.0 (Single Minute Exchange of Die- SMED 4.0)
Chuyển đổi nhanh (SMED) là một trong những công cụ của hệ thống quản lý tinh gọn. Trong sản xuất, việc thay đổi dụng cụ và khuôn mẫu mất một khoảng thời gian đáng kể. Trong khi đang thay đổi dụng cụ hoặc khuôn mẫu, dây chuyền sản xuất phải ngừng hoạt động, dẫn đến mất thời gian và các chi phí liên quan. Ngoài ra, “thời gian chết” để thay đổi dụng cụ hoặc khuôn đúc gây ảnh hưởng đến các quyết định sản xuất khác.
SMED giúp giảm thời gian chuyển đổi thiết bị khi sản xuất từ sản phẩm này sang sản phẩm khác trong một quá trình sản xuất. Khi sản phẩm cuối cùng của dòng sản phẩm A được hoàn thành sản xuất, máy móc thiết bị trong hệ thống cần được dừng lại, khóa an toàn, dây chuyền sản xuất được bảo dưỡng sạch sẽ. Các dụng cụ được tháo ra và các dụng cụ mới sẽ được lắp đặt để sản xuất dòng sản phẩm B kế tiếp. Khi đó, thời gian dừng máy được xem là “thời gian chết”, không tạo ra giá trị (Non Value Added). Khoảng thời gian này có thể được cải tiến thông qua SMED. Hơn nữa là giảm đến “single-minute”, tức là giảm thời gian chuyển đổi xuống số phút chỉ còn là một con số, hay nói cách khác là giảm hẳn xuống dưới 10 phút.
Nyhuis et al. xác định các công nghệ trong Công nghiệp 4.0 để cung cấp thông tin hỗ trợ giảm thời gian thay đổi dụng cụ hoặc khuôn đúc để chuyển từ sản xuất sản phẩm này sang sản phẩm khác.
Ngoài AR và plug and play, sản xuất in 3D (additive manufacturing, AM) dự kiến sẽ tác động đến việc giảm khoảng “thời gian chết” này. Quy trình sản xuất in 3D làm giảm tối thiểu thời gian để lựa chọn, tìm kiếm và điều chỉnh các công cụ để sản xuất sản phẩm. Tuy nhiên, một số thay đổi trong quá trình sản xuất in 3D vẫn xảy ra như điều chỉnh nhiệt độ, hoạt động làm sạch hệ thống… Do đó, Feldmann và Gorji cho rằng SMED cũng có thể được áp dụng cho sản xuất in 3D. Tuy nhiên, tác động của SMED tới sản xuất in 3D dự kiến sẽ khá nhỏ vì yếu tố “thời gian chết” đã giảm đến mức tối thiểu.
7. Quản lý trực quan 4.0 (Visual Management 4.0)
Quản lý trực quan là sử dụng các công cụ mang tính trực quan mà con người có thể quan sát và nhìn thấy được nội dung cần thực hiện cũng như thấy được ý nghĩa của nó. Mục đích của quản lý trực quan là chỉ dẫn công việc thông qua các hình ảnh… nhằm giúp người lao động nắm bắt nhanh thông tin sản xuất, các hướng dẫn công việc. Không những vậy nó còn giúp cho người quản lý quản lý đơn giản hơn và hiệu quả hơn.
Mục đích của Quản lý trực quan là tăng cường tính minh bạch. Điều này sẽ thực hiện được thông qua chuyển các mục tiêu, tiêu chuẩn và thông số kỹ thuật thành các thông tin trực quan. Tầm quan trọng của Quản lý trực quan ngày càng tăng khi lượng dữ liệu trong quá trình sản xuất tăng lên. Các phương thức để thực hiện Quản lý trực quan là 5S, phân vùng và andon.
5S là một cách tiếp cận có hệ thống để tổ chức nơi làm việc và nhằm mục đích cải thiện sự rõ ràng thông qua việc giữ cho không gian làm việc sạch sẽ và sắp xếp các công cụ một cách hợp lý. Do đó, lãng phí được loại bỏ ở nơi làm việc. Auto-ID và AR có thể hỗ trợ thực hiện 5S hiệu quả hơn. RFID đảm bảo nhận dạng và “đánh dấu” các đối tượng để giúp giảm thời gian tìm kiếm.
Phân vùng cho phép đánh dấu điểm đến bằng cách sử dụng phương tiện trực quan. Việc sử dụng màu sắc làm tăng giá trị thông tin. Phân vùng có một số nhược điểm trong đó, phương pháp này không phù hợp để điều chỉnh sản xuất linh hoạt. HCI và AR giúp khắc phục sự thiếu linh hoạt này. Koch và cộng sự, Neges et al. mô tả một hệ thống để điều hướng bằng phương tiện AR dựa trên các dấu hiệu tự nhiên như các dấu hiệu cảnh báo.
Andon được áp dụng để hình dung tình trạng và sự gián đoạn trong sản xuất và do đó hỗ trợ nguyên tắc quản lý tinh gọn jidoka. Ngoài ra, bảng andon hiển thị giá trị thực tế và mục tiêu để hiển thị độ lệch. Đối với bảng andon kỹ thuật số, một số nhà cung cấp giải pháp đã thực hiện trực quan hóa dữ liệu và quy trình phức tạp theo thời gian thực. Ví dụ về dữ liệu liên quan là tình trạng máy, tiến độ sản xuất, trạng thái đơn hàng và việc sử dụng công suất. Lấy thông tin này từ các thiết bị di động hỗ trợ truy cập và sử dụng độc lập với vị trí.
8. Poka-yoke 4.0
Poka-yoke được dịch ra là “chống sai lỗi” hay “ngăn ngừa lỗi vô ý”, được đặt ra với mục đích để loại bỏ các lỗi trong sản xuất bằng cách hướng sự chú ý đến những lỗi hay mắc phải nhất. Người sáng tạo ra khái niệm Poka-yoke là một kỹ sư tên là Shigeo Shingo. Ông đã phát triển và ứng dụng Poka-yoke trong các dây chuyền sản xuất lắp ráp của hãng xe hơi Toyota, giúp hạn chế tối đa các sai phạm mà công nhân thường xuyên mắc phải.
Poka-yoke mô tả các cơ chế giúp người vận hành tránh sai lầm. Do đó, nó thúc đẩy việc phát hiện và loại bỏ các điều kiện bất thường để ngăn chặn các sản phẩm bị lỗi rời khỏi quy trình. Điều này đặc biệt quan trọng trong các ngành công nghiệp với nhiều loại sản phẩm. Poka -yoke được nhận ra bằng cách tạo ra các chuỗi bắt buộc hoặc bằng cách xem xét quá trình trong quá trình thực thi và dừng lại trong trường hợp xảy ra lỗi. [F. Brunner, Japanische Erfolgskonzepte: KAIZEN, KVP, Lean Production Management, Total Productive Maintenance, Shopfloor Management, Toyota Production System GD3 - Lean Development, 2nd ed. München, Germany: Hanser, 2011]
Auto-ID đảm bảo nhận dạng và gán chính xác. Bộ nhớ sản phẩm kỹ thuật số cho phép các thành phần cần thiết và giúp xác định việc giao hàng không chính xác. Bằng cách sử dụng các cảm biến thông minh và học máy, máy móc có thể tự động điều chỉnh các bất thường để đảm bảo chất lượng sản phẩm tối ưu. AR và đầu đọc RFID có thể được sử dụng để thực hiện lựa chọn “không xảy ra lỗi”./.
TS. Hà Minh Hiệp, Phó Tổng cục trưởng Tổng cục TCĐLCL
Bình luận
Nổi bật
Tăng tốc năng suất cho doanh nghiệp thiết kế đồ họa và in ấn nhờ công cụ Kanban
sự kiện🞄Chủ nhật, 31/08/2025, 09:11
(CL&CS) – Hiện nay, việc tối ưu hóa quy trình làm việc đã trở thành yếu tố sống còn để nâng cao năng suất và chất lượng sản phẩm. Công cụ Kanban đã và đang chứng minh là một giải pháp hiệu quả giúp các doanh nghiệp trong lĩnh vực này không chỉ quản lý công việc trơn tru hơn mà còn tạo ra sự linh hoạt, minh bạch trong toàn bộ chu trình sản xuất.
KPI – Đòn bẩy nâng cao năng suất và chất lượng trong ngành sản xuất vận tải
sự kiện🞄Thứ sáu, 29/08/2025, 07:21
(CL&CS) - Hiện nay, các doanh nghiệp ngành sản xuất vận tải tại Việt Nam đang đứng trước áp lực lớn về năng suất, chi phí và chất lượng dịch vụ. Để duy trì vị thế và phát triển bền vững, nhiều đơn vị đã lựa chọn các công cụ quản trị hiện đại nhằm tối ưu hoạt động sản xuất, kinh doanh. Trong đó, KPI (Key Performance Indicator - Chỉ số đo lường hiệu quả công việc) đã và đang là một phương pháp khoa học, mang lại hiệu quả rõ rệt trong quản lý và điều hành.
Áp dụng Six Sigma giúp nâng tầm năng suất và chất lượng cho doanh nghiệp điện tử
sự kiện🞄Thứ năm, 28/08/2025, 14:01
(CL&CS) - Xu thế hiện nay, người tiêu dùng ngày càng khắt khe, đòi hỏi thiết bị điện tử phải vừa tinh xảo, bền bỉ, vừa tích hợp nhiều tính năng mà vẫn giữ mức giá cạnh tranh. Để đáp ứng yêu cầu này, nhiều doanh nghiệp đã tìm đến những công cụ quản lý chất lượng hiện đại. Trong số đó, Six Sigma đã và đang như một giải pháp hiệu quả, giúp doanh nghiệp điện tử loại bỏ sai lỗi, tối ưu quy trình, đồng thời tạo ra lợi thế cạnh tranh bền vững.
anh đứcLorem ipsum dolor sit amet, consectetur adipisicing elit. Quis cum, ut esse cupiditate autem. Dolor est dolorem sunt, sequi omnis corporis cumque ratione accusamus ex deserunt, molestiae consequuntur natus beatae.